What is a Master Production Schedule (MPS) In Detail?
A Master Production Schedule (MPS) is a high-level plan that outlines the specific products, quantities, and timeframes for production within a manufacturing organization. It bridges the gap between sales forecasts and the production process, acting as a central source of information for various departments. Learn SAP modules, improve your business sense, and advance your career with SAP Course in Pune at Connecting Dots ERP.
In the ever-evolving world of manufacturing, efficiency reigns supreme. To navigate the complexities of production planning and ensure smooth operations, manufacturers rely on a crucial tool: the Master Production Schedule (MPS). Linking production with consumer demand while taking into account the limitations and capabilities of the production facilities is the goal of MPS.
What is a Master Production Schedule (MPS)?
The MPS serves as a roadmap for production by outlining what products need to be manufactured, in what quantities, and when they need to be completed. It bridges the gap between sales forecasts and the actual production process, acting as a single source of truth for various departments within the organization.
Registration Link: https://connectingdotserp.in/
Call Now: 9004002958 / 9004001938
Key Components of a MPS:
- Products: The MPS identifies the specific products or finished goods slated for production. This information typically aligns with the company’s product portfolio or a subset of high-demand items.
- Quantities: The MPS (Master Production Schedule) actively determines the specific quantity to be produced for each product within a predetermined period.
- Time Periods: The MPS typically spans a specific timeframe, often ranging from a few months to a year. Depending on the production lead time and planning needs, the timeframe is divided into smaller periods, such as weeks or months.
The Benefits of Implementing a MPS:
An effectively implemented MPS offers a multitude of benefits for manufacturing businesses, including SAP courses and classes in Pune:
- Enhanced Production Planning: By providing a clear roadmap, the MPS empowers manufacturers to plan their production activities efficiently. It facilitates the allocation of resources, such as personnel, materials, and equipment, to meet production targets.
- Improved Inventory Management: The MPS aids in maintaining optimal inventory levels by balancing production output with anticipated demand. This helps minimize overstocking, which can tie up valuable resources, and prevent stockouts, which can lead to production delays and customer dissatisfaction.
- Increased Visibility and Coordination: The MPS fosters transparency across various departments, including sales, production, and purchasing. Improved visibility enables better coordination and collaboration, ensuring alignment with the production plan.
- Reduced Lead Times: By streamlining production planning and resource allocation, the MPS can contribute to shorter lead times. This allows businesses to respond to customer demands more effectively and gain a competitive edge.
- Improved On-Time Delivery: A well-defined MPS paves the way for smoother production processes and efficient material procurement. This translates to fewer delays and disruptions, ultimately leading to higher on-time delivery rates.
Registration Link: https://connectingdotserp.in/
Call Now: 9004002958 / 9004001938
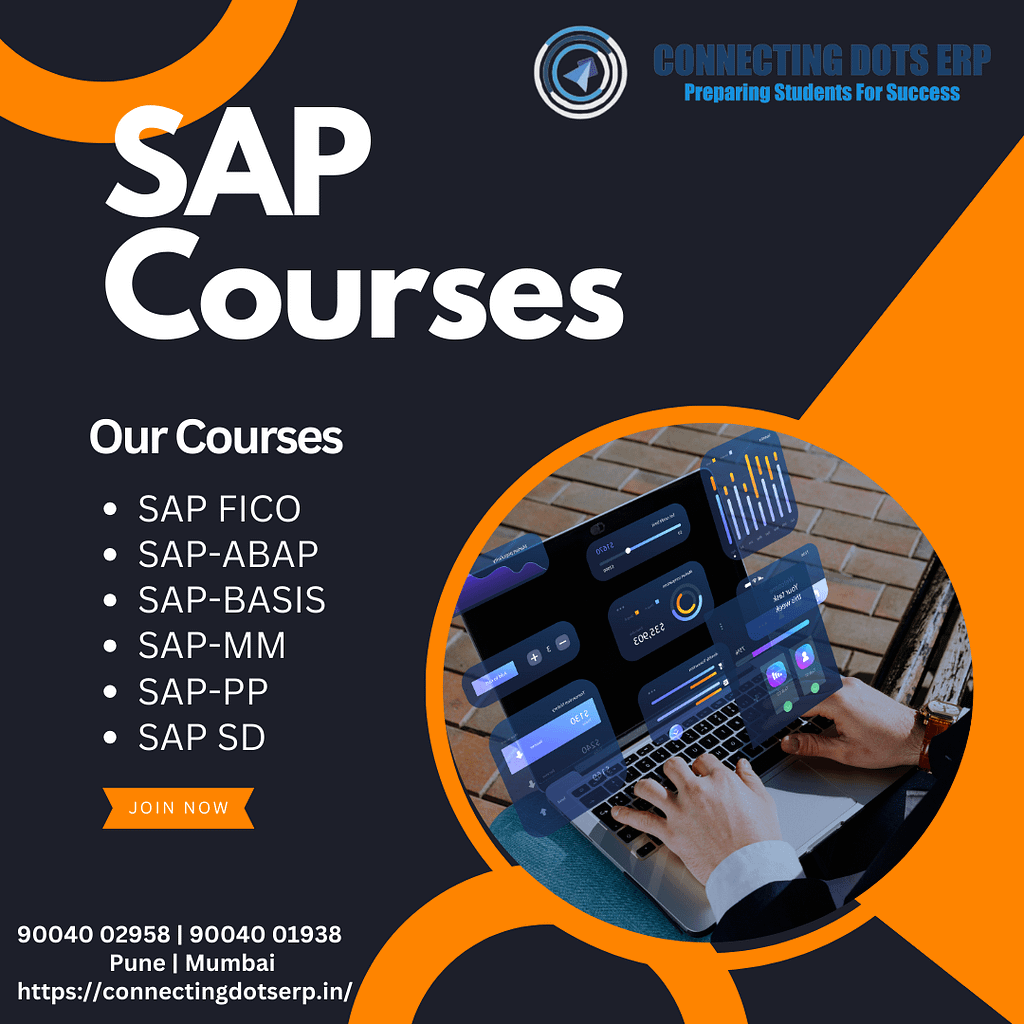
Developing an Effective Master Production Schedule:
Creating a robust MPS involves a series of crucial steps:
- Gathering Input: The process begins by gathering inputs from various sources, including sales forecasts, historical demand data, and production lead times.
- Demand Forecasting: Sales forecasts are used by the MPS to identify the products and quantities to be included. Businesses can leverage various forecasting techniques, such as moving averages or exponential smoothing, to predict future demand trends.
- Inventory Management: To avoid production bottlenecks or shortages, you need to factor in existing inventory levels and lead times for raw materials and components.
- Production Capacity Planning: Assessing available production capacity, including labor, equipment, and facility limitations, is crucial to ensure the feasibility of the MPS.
- MPS Generation: Using the gathered data and insights, the MPS is generated, outlining the specific products, quantities, and timeframes for production. Software programs can be employed to simplify and automate the MPS creation process.
- Ongoing Monitoring and Adjustments: The MPS is not a static document. It needs to be continuously monitored and adjusted to reflect any changes in demand, production capacity, or other relevant factors.
Looking to Learn More?
Consider enrolling in an SAP class in Pune if you want to delve deeper into production planning and master the intricacies of creating and managing an MPS. Manufacturing and supply chain management widely use SAP software, and understanding its functionalities related to production planning can be immensely valuable. By acquiring the necessary skills and knowledge, you can gain a competitive edge in the manufacturing industry and contribute to optimizing production processes effectively.